Troubleshooting Air Leaks
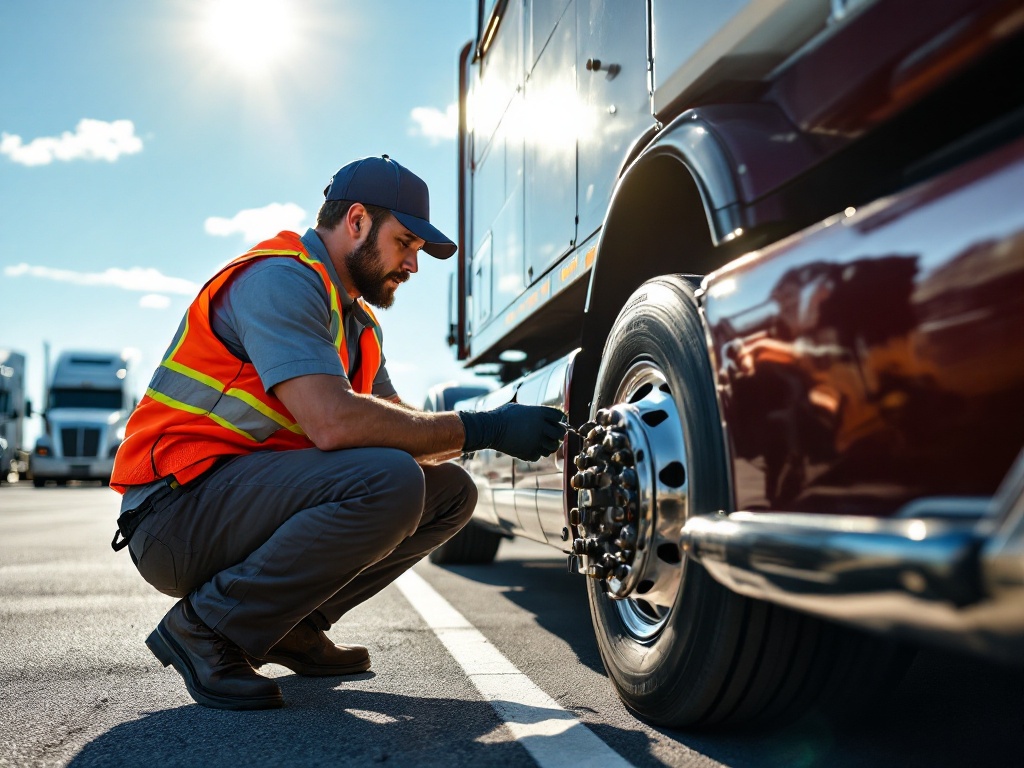
Did you know that air leaks can reduce a semi truck’s braking efficiency by up to 30%? This alarming statistic underscores the importance of regular inspections and repairs. You might think identifying these leaks is straightforward, but the reality is often more complex than it appears. Understanding how to effectively detect and fix these issues can not only enhance your truck’s safety but also save you from unexpected downtime and expenses. So, what steps should you take to guarantee your vehicle stays in top condition?
Preparing for the Inspection
Preparing for the inspection of your semi truck’s air brake system is vital for guaranteeing safety and performance. First, verify the engine’s turned off to prevent accidental starts during your inspection. Next, release all air pressure from the system by depressing the brake pedal or using the air release valve. Before diving in, check the vehicle’s manual for specific instructions on preparing the air brake system.
Gather all necessary safety equipment, including gloves and safety glasses, and confirm they’re in use. Clear the area around the vehicle to eliminate any obstacles or hazards that could interfere with your inspection process. Additionally, ensure you have a way to monitor governor cut-off at approximately 120 PSI during your pressure checks to confirm proper air system functionality. Using the TP-9367 Marksman™ II ultrasonic tool will enhance your ability to detect air brake leaks accurately.
You’ll need tools like soapy water or a leak detection solution to identify leaks through bubble formation. A pressure gauge is important for monitoring air pressure levels, while a leak detection tool such as the TP-9367 Marksman™ II will give you precise detection capabilities.
Additionally, have wrenches and pliers ready for inspecting fittings and connections. By following these steps, you empower yourself to maintain a safe and compliant air brake system, guaranteeing your semi truck performs efficiently on the road.
Conducting the Leak Test
To conduct the leak test, begin by building up the air pressure to the recommended level, typically 120 PSI. Once the pressure stabilizes, monitor the gauges closely to guarantee the drop in pressure remains within acceptable limits for your vehicle type. Accurate pressure monitoring is essential for identifying any potential leaks in the system. Proper air pressure levels must be maintained during tests, as employers have specific experience requirements to ensure safety and compliance in the trucking industry. Additionally, the air brake leak test is critical, as failure during this test results in automatic failure.
Leak Test Procedure
Conducting a leak test on your semi truck’s air system is essential for guaranteeing ideal performance and safety. Start by building air pressure to the operating levels, typically between 90-125 PSI, then shut off the engine.
Select a gear and turn the ignition switch to the on position without starting the engine. Release the parking and trailer brakes, allowing the air pressure to stabilize before checking for air loss.
For a static leak test, monitor the air pressure for one minute; it shouldn’t drop more than 2 PSI for straight trucks and 3 PSI for combination vehicles. Brake system failures account for a significant portion of out-of-service violations, making this test crucial for maintaining compliance and safety. Additionally, regularly checking the air pressure and leak status can prevent potential issues.
In a dynamic leak test, with the engine off, apply the foot brake to pressurize the brake system at around 90 PSI. Hold the brake down and check the pressure drop—no more than 3 PSI for straight trucks and 4 PSI for combination vehicles.
Consider using automated leak detection equipment like the NanoLeak Finder for precision. Run a two-minute test to determine leak-down rates and pinpoint leaks with sniffing devices.
After repairs, conduct a secondary test to validate that the system holds pressure effectively. Regular testing guarantees your air system remains leak-free, enhancing safety and performance.
Pressure Monitoring Techniques
How can you effectively monitor air pressure during a leak test on your semi truck? Start by building the air pressure to 120 PSI or more. After releasing the truck and trailer brakes, verify the pressure stabilizes.
Run the engine at full-governed RPM to build pressure from 85 to 100 PSI in 40 seconds or less. Then, turn off the engine and switch on the ignition to monitor your gauges.
Here are three critical steps for monitoring pressure drop:
- Timing the Drop: With the engine off, release the service brake and time how quickly the air pressure drops. Aim for a loss of less than 2 PSI in one minute for single vehicles and less than 3 PSI for combinations.
- Identifying Thresholds: If your pressure drop exceeds 2 PSI (single) or 3 PSI (combination) in one minute, there’s a leak that needs immediate attention.
- **Using *Detection Methods***: Apply soapy water to connections or utilize an ultrasonic leak detector to pinpoint leaks efficiently. Regular inspection of brake components is essential to ensure your semi truck remains safe and reliable on the road. Additionally, ensure that your air loss rates comply with maximum allowable limits to prevent potential safety hazards.
These techniques guarantee your semi truck remains safe and reliable on the road.
Identifying Leak Locations
To effectively identify leak locations on your semi-truck, you can utilize smoke leak detection, the soapy water technique, and ultrasound leak analysis. Each method provides a unique advantage, whether it’s visual confirmation with bubbles, swift detection with smoke, or precision measurement through sound waves. Additionally, identifying air leaks by inspecting fittings and connections can further enhance your leak detection efforts. Regular inspections can help maintain air brake integrity and prevent unexpected failures.
Smoke Leak Detection
Identifying air leaks in a semi truck is vital for maintaining ideal performance and fuel efficiency. One effective method for pinpointing these leaks is using the HD PowerSmoke™ machine. This heavy-duty smoke machine, designed specifically for semi-trucks, can help you accurately locate leaks in a matter of minutes.
Here are three key features of the PowerSmoke™ that enhance its effectiveness:
- Variable Pressure and Flow: You can adjust the pressure from 2 to 20 PSI, simulating various operational conditions to reveal even the smallest leaks.
- Rapid Diagnostics: The machine utilizes a sniffing device that detects unique smoke signatures, allowing for quick identification of leak sources.
- Automated Testing: By initiating automated tests, you minimize human error, freeing up your time to focus on other important tasks.
As smoke exits through cracks or holes, it provides a clear visual cue for where repairs are needed.
In addition, after repairs, you can conduct an Air Leak Decay test to verify that the system holds pressure effectively, confirming the integrity of your work.
This precision leads to improved performance and efficiency, significant for any trucking operation.
Soapy Water Technique
After successfully detecting leaks with the HD PowerSmoke™ machine, you can further enhance your inspection process by employing the soapy water technique.
Start by preparing a solution of water mixed with a small amount of liquid dish soap or mild detergent. If you’re using concentrated soap, remember to use less to avoid an overly thick solution. For stronger bubbles, consider adding glycerine or corn syrup. Using a spray bottle, apply the solution effectively.
Next, shut off the truck and release air from the system. Focus on connections, joints, and fittings, particularly around air hoses and valves. Spray the soapy water generously on these suspected areas.
Watch closely for bubble formation, which indicates leaks. If you don’t see bubbles immediately, reapply the solution and inspect from different angles. Begin at low pressure to prevent blowing the soap away.
Large or frequent bubbles signify severe leaks, so mark each location for tracking. If you detect a leak, shut off the air supply and repair it promptly.
After repairs, conduct a follow-up test to confirm no leaks remain, replacing any faulty components as necessary. This technique is essential for maintaining your truck’s air system integrity.
Ultrasound Leak Analysis
Many technicians find that using ultrasound leak analysis greatly enhances the accuracy and efficiency of locating air leaks in semi-truck systems.
By employing specialized tools like the CABIN-SAFE™ or the FLIR Si124 ultrasound camera, you can detect leaks that traditional methods often miss. These tools convert ultrasonic signals into audible sounds or visual representations, making it easier to identify issues.
Here are three key steps in the ultrasound leak detection process:
- Pressurize the System: Start by pressurizing the air system to at least 90 psi. This facilitates the detection of escaping air.
- Scan for Leaks: Use the ultrasonic tool to scan the exterior of the vehicle. The FLIR Si124 camera, equipped with 124 microphones, filters out background noise to focus on leak frequencies.
- Verify Locations: After identifying potential leaks, confirm their locations by conducting a sensitivity test or utilizing the ultrasound camera for precise mapping.
Utilizing these advanced tools not only reduces detection time considerably but also minimizes human error, ensuring that your semi truck remains compliant with safety standards and operationally sound.
Common Causes of Leaks
Understanding the common causes of air leaks in a semi-truck is essential for maintaining ideal performance and safety. Identifying these issues early can prevent costly repairs and guarantee your truck operates efficiently.
Cause | Description | Prevention |
---|---|---|
Poor Initial Installation | Incorrect component installation leads to gaps. | Always use quality parts and guarantee proper installation. |
Corrosion and Environment | Road treatments and weather can cause corrosion. | Regularly inspect and protect components from harsh conditions. |
System Contamination | Oil, water, and dirt can corrode components. | Maintain high-quality air dryers and filters to keep the system clean. |
Wear and Tear | Brake components degrade over time, causing leaks. | Perform regular inspections and replace worn parts promptly. |
Repairing the Leaks
Repairing air leaks in a semi-truck is essential for maintaining ideal performance and safety. Start by shutting off the truck and releasing air pressure. Depress the brake pedal to drain the system and bleed the air lines to avoid any loud noises during repair.
Use leak detection tools to locate the leaks and inspect all fittings and connections for signs of damage.
Follow these steps for effective repairs:
- Detach the air hose/line: Disconnect the hose from the system using the appropriate fittings.
- Replace with new fittings: Trim any damaged sections of the hose and install compatible brass or nylon fittings for durability.
- Secure connections: Verify each new fitting is fully seated to prevent future leaks.
For emergency situations, temporary fixes like tape and zip ties can help, but rely on them only until you reach a service station.
Verifying Repairs
Once you’ve completed the repairs, it’s essential to conduct a secondary air leak test to guarantee no residual leaks exist.
Check the functionality of safety devices, like low air warnings, to confirm they respond at the correct pressure levels.
Finally, perform visual and auditory inspections around the repaired areas to catch any leaks that may not have been addressed.
Secondary Air Leak Test
After completing repairs to the secondary air system, you need to verify the effectiveness of your work through a Secondary Air Leak Test. This process guarantees that your repairs hold up under operational conditions.
Here’s how to conduct the test effectively:
- Prepare the System: Drain the vehicle air tanks by repeatedly pumping the brakes. Remove the air dryer fill port plug and connect a dial pressure gauge.
Start the vehicle to fully pressurize the tanks, then turn it off when the compressor shuts off. Allow the system to stabilize for 10 minutes.
- Monitor Pressure: Note the initial air pressure and start a timer. Over the next few minutes, pay close attention to any pressure drops.
A significant drop indicates a leak that needs further investigation.
- Identify and Verify: Utilize soapy water to check for bubbles at connections, fittings, and suspect areas.
If leaks are found, repair them, then re-pressurize the system and retest. Confirm all components are securely connected and functioning properly.
Safety Device Functionality
Verifying the functionality of safety devices in the air brake system is essential to guarantee ideal performance and reliability. Start by utilizing the Air Brake NanoLeak Finder™ for automated leak detection. Connect this tool to the main air-holding tank and conduct a two-minute test to check for leak-down. The machine pressurizes the system with “signature air,” confirming accurate diagnostics while adhering to US DOT standards.
Next, perform pressure tests to confirm that the air brake system doesn’t leak down more than 5 psi in 60 seconds. Use the Smoke Monster Pro S 2000HD Heavy Duty to switch to the Air Leak Decay test, verifying that pressure holds post-repair. Conduct these tests at a minimum of 90 psi for effective leak localization.
After repairs, use the sniffing device from the NanoLeak Finder, starting at a lower sensitivity to locate smaller leaks. Re-run the automated test to confirm successful fixes.
Ascertain all components are installed per manufacturer guidelines, utilizing specialty tools for precise cuts on brake hoses. Consistent verification guarantees your air brake system remains safe and functional, allowing you to drive with confidence.
Visual and Auditory Inspection
Thorough visual and auditory inspections are critical for confirming repairs to the air brake system on a semi truck.
Begin by systematically inspecting the entire air brake system. Look for worn or damaged parts, paying close attention to chafed components and improperly routed air lines.
Next, listen for hissing noises, indicating air leaks, while the parking brake is set and the brake pedal is pressed. This dual approach enhances your ability to pinpoint issues accurately.
Here are three key steps to follow:
- Visual Inspection: Examine the air compressor drive belt for tension and wear, and check all connections for cracks or looseness.
- Auditory Inspection: Walk around the truck when it’s above 100 PSI, listening for any unusual sounds that could indicate escaping air.
- Soapy Water Method: Apply a soapy water mixture to fittings and connections to reveal small leaks through bubbling.
Tools for Leak Detection
Effective leak detection is essential for maintaining the performance and safety of a semi truck’s air systems. To achieve this, you can utilize advanced tools designed specifically for leak detection.
The Air Brake NanoLeak Finder™ stands out, diagnosing leaks in high-pressure air brake and suspension systems with its innovative vapor technology. It offers live graphing and data logging, ensuring you get precise results.
Another excellent option is the Marksman™ II Ultrasonic Diagnostic Tool. This device converts inaudible sounds into audible ones, making it easy for you to pinpoint leaks quickly. It works by identifying friction created as pressurized air escapes, ensuring accurate diagnoses across various fluid systems.
For a simpler, more manual approach, the soapy water method is highly effective. By mixing dish soap with water and applying it to suspected leak sites, you can visually identify leaks through the formation of bubbles.
Additionally, having gladhand adaptors on hand can facilitate effective testing and repairs. These tools are essential for ensuring your semi truck’s air systems remain efficient and reliable, ultimately enhancing your safety on the road.
Safety Protocols to Follow
Safety protocols are essential when inspecting and repairing air leaks on a semi truck to guarantee both your safety and the vehicle’s reliability. Following these protocols confirms that you minimize risks while effectively addressing air leaks.
- Pre-Inspection Measures: Always park the vehicle on a level surface and engage the parking brake.
Check the low air pressure warning device for proper function and wear appropriate personal protective equipment (PPE), like gloves and safety glasses, to protect yourself during the inspection.
- Leak Detection Safety: Build air pressure to 90-100 psi to facilitate leak detection.
Use smoke machines or soapy water solutions without foreign substances for testing. During your inspection, listen for audible leaks and wiggle hoses to uncover hidden issues.
- Repair and Testing: After repairs, perform an air brake leak-down test to confirm system integrity.
Confirm that all connections are secure and free from debris. A thorough final walk-around inspection will help you catch any remaining audible leaks before finishing your work.
Maintenance Tips for Prevention
Regular maintenance is essential for preventing air leaks in your semi truck’s brake system. Start with a quick 2- to 3-minute walk-around inspection before each trip. Listen for audible leaks, especially during tire checks, and visually inspect the entire air brake system, including fittings, connections, and hoses.
Pay special attention to gladhand seals, as these are common leak points. If you notice the system charges more frequently or takes longer to charge, you may have a leak.
Annually replace air dryer cartridges with original equipment to avoid moisture-related corrosion. Ascertain all fittings and lines are installed per the manufacturer’s recommendations, and opt for durable brass fittings over nylon.
Regularly check for damaged fasteners and torque them to specifications. Implement a winter-prep regimen to combat corrosion from de-icing treatments, and conduct post-winter inspections.
Use corrosion-resistant materials wherever possible and keep the air brake system clean. Finally, carry leak detection tools, such as soapy water or specialized tools, to locate any leaks.
Always verify repairs with secondary tests like the Air Leak Decay test, making certain your system remains leak-free and ready for the road.
Importance of Regular Inspections
Conducting regular inspections of your semi truck’s air brake system is essential for maintaining ideal performance and safety.
These inspections allow you to catch air leaks early, preventing more severe issues that can lead to costly repairs and downtime.
By prioritizing inspections, you guarantee your vehicle remains compliant with DOT standards and minimizes the risk of accidents.
Here are three key reasons for regular inspections:
- Early Detection: Identify air leaks before they escalate into significant problems, guaranteeing that your truck stays operational and compliant with safety regulations.
- Enhanced Safety: Regular checks maintain reliable braking performance, safeguarding not only your vehicle but also the safety of other road users by preventing potential accidents.
- Cost Efficiency: Timely inspections reduce the need for extensive repairs, saving both time and money.
They help avoid unexpected breakdowns, keeping your truck on the road and maximizing productivity.
Frequently Asked Questions
How Often Should I Inspect for Air Leaks?
You should inspect every three months with visual checks, while thorough inspections occur every six months or after 100,000 miles. Frequent checks guarantee safety, reliability, and freedom from unexpected issues while you’re on the road.
Can I Perform These Tests Myself?
Yes, you can perform these tests yourself. Confirm you have the right tools, follow safety protocols, and adhere to guidelines. Regular inspections empower you to maintain your vehicle’s efficiency and confirm safe operation on the road.
What Are the Signs of an Air Leak?
You might think identifying air leaks is complex, but it’s not. Listen for high-pitched sounds, check for pressure drops, and inspect connections for bubbles. Regular checks guarantee safety and performance, so stay proactive.
How Long Does the Repair Process Take?
The repair process typically takes about one to three hours, depending on the leak’s complexity. You’ll need to inspect, disconnect, replace components, and conduct tests to guarantee everything’s sealed properly and functioning efficiently.
Will Air Leaks Affect My Fuel Efficiency?
Yes, air leaks negatively impact your fuel efficiency. They force your engine to work harder, consuming more fuel for the same output. Regular inspections and repairs are essential to maintain peak performance and minimize operating costs.
Conclusion
To summarize, regularly inspecting and repairing air leaks on your semi-truck is crucial for safety and performance. Did you know that even a small air leak can lead to a 30% loss in braking efficiency? By staying proactive, you not only enhance your truck’s reliability but also reduce the risk of costly breakdowns. Make inspections a routine to guarantee your vehicle remains roadworthy, keeping both you and others safe on the road.